About Us
- Company
- Customers
- Technical Highlights
- Advantages
- Company History
- Environmentally-friendly Facility
- Patents
- Quality Control
- R&D
- Mucking Loader Manual
- Mucking Loader Technical Description
- Mucking Loader Operation Description
- Mucking Loader Maintenance
- Mucking Loader Operation Notes
- Roadheader Manual
- Roadheader Technical Description
- Roadeheader Maintenance
- Roadheader Notes
- Roadheader Operating Method
- Mine Shuttle Car Manual
- Mine Shuttle Car Maintenance
- Mine Shuttle Car Operation
- Mine Shuttle Car Technical Description
- Mine Shuttle Car Notes
- Trolley Locomotive Maintenance
- Maintenance Manual of Drilling Jumbo
- Contact Us
Mucking Loader Operation Notes
1. Keep personnel and device away from the working haggloader to
prevent potential accident.
2. Clean hard materials larger than 250mm where the haggloader moves.
3. The length of electric cable should be decided as per specific needs. Keep personnel away when reeling the cable to prevent stumble. No squeeze is allowed.
4. The haggloader should be kept 50 meters away from the explosion position.
5. Park the haggloader with the bucket and the small arm gently touching the stop block, lower the large arm to let the bucket teeth touch the earth, lower the transporting trough to its lowest. Retract the push plate for walking convenience.
6. Put a triangle wood under the crawler belt to prevent it from sliding down the slope.
7. Turn off the power when parking.
8. Idle the pump 5-10 minutes if the downtime is beyond four hours.
9. Rise the temperature by idling the pump if the oil tank is below 25°C in winter.
10. Start the draught fan, pilot pump and main pump every five seconds. The drought fan can be turned off separately after the whole haggloader is started.
11. Stop for cooling if the temperature of the oil tank reaches 55°C or the return oil temperature reaches 80°C.
12. Regular change of the hydraulic oil
(1) The first oil change should happen after running the machine 100 hours, second change after 600 hours, and from the third time on change the oil every 600 working hours.
(2) Change the oil one time per year, and clean or replace the hydraulic oil filter core.
Notes of changing the hydraulic oil
(1) If the oil clogging indicator of the control cabinet turns on, clean or replace the magnetic rod of the scavenge filter, the core of the oil absorption filter and the oil filling filter.
(2) The clogging indicator alarm will turn red if the oil filling filter is clogged.
(3) Both the oil return and absorption filters are equipped with self-sealing valve to prevent the oil from flowing out even when the end cover is dismantled.
(4) Bypass valve is equipped to prevent the oil pump from suctioning only the air when clog happened.
(5) Make on-time clean and replacement, or else the whole oil circuit will get damaged.
13. Warranty Period
(1) The warranty period is six months from the date of pilot operating.
(2) On-site assembly should be no later than three months after delivery.
(3) After 300, 600 and 900 working hours, maintenance will only be carried out within two weeks after the designated engineer has delivered to the supplier the report.
14. Regular parts such as the filter and its core, lubricating oil, hydraulic oil and wear parts are not within the warranty.
15. Electric bell is used as warning signal when the mucking loader moves forward or backward.
2. Clean hard materials larger than 250mm where the haggloader moves.
3. The length of electric cable should be decided as per specific needs. Keep personnel away when reeling the cable to prevent stumble. No squeeze is allowed.
4. The haggloader should be kept 50 meters away from the explosion position.
5. Park the haggloader with the bucket and the small arm gently touching the stop block, lower the large arm to let the bucket teeth touch the earth, lower the transporting trough to its lowest. Retract the push plate for walking convenience.
6. Put a triangle wood under the crawler belt to prevent it from sliding down the slope.
7. Turn off the power when parking.
8. Idle the pump 5-10 minutes if the downtime is beyond four hours.
9. Rise the temperature by idling the pump if the oil tank is below 25°C in winter.
10. Start the draught fan, pilot pump and main pump every five seconds. The drought fan can be turned off separately after the whole haggloader is started.
11. Stop for cooling if the temperature of the oil tank reaches 55°C or the return oil temperature reaches 80°C.
12. Regular change of the hydraulic oil
(1) The first oil change should happen after running the machine 100 hours, second change after 600 hours, and from the third time on change the oil every 600 working hours.
(2) Change the oil one time per year, and clean or replace the hydraulic oil filter core.
Notes of changing the hydraulic oil
(1) If the oil clogging indicator of the control cabinet turns on, clean or replace the magnetic rod of the scavenge filter, the core of the oil absorption filter and the oil filling filter.
(2) The clogging indicator alarm will turn red if the oil filling filter is clogged.
(3) Both the oil return and absorption filters are equipped with self-sealing valve to prevent the oil from flowing out even when the end cover is dismantled.
(4) Bypass valve is equipped to prevent the oil pump from suctioning only the air when clog happened.
(5) Make on-time clean and replacement, or else the whole oil circuit will get damaged.
13. Warranty Period
(1) The warranty period is six months from the date of pilot operating.
(2) On-site assembly should be no later than three months after delivery.
(3) After 300, 600 and 900 working hours, maintenance will only be carried out within two weeks after the designated engineer has delivered to the supplier the report.
14. Regular parts such as the filter and its core, lubricating oil, hydraulic oil and wear parts are not within the warranty.
15. Electric bell is used as warning signal when the mucking loader moves forward or backward.
Related Products
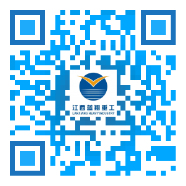