About Us
- Company
- Customers
- Technical Highlights
- Advantages
- Company History
- Environmentally-friendly Facility
- Patents
- Quality Control
- R&D
- Mucking Loader Manual
- Mucking Loader Technical Description
- Mucking Loader Operation Description
- Mucking Loader Maintenance
- Mucking Loader Operation Notes
- Roadheader Manual
- Roadheader Technical Description
- Roadeheader Maintenance
- Roadheader Notes
- Roadheader Operating Method
- Mine Shuttle Car Manual
- Mine Shuttle Car Maintenance
- Mine Shuttle Car Operation
- Mine Shuttle Car Technical Description
- Mine Shuttle Car Notes
- Trolley Locomotive Maintenance
- Maintenance Manual of Drilling Jumbo
- Contact Us
Maintenance Manual of Drilling Jumbo
A. Daily or frequently required maintenance
1. Check if there is any oil leakage.
2. Fasten loosened bolts.
3. Clean the propelling beam.
4. Check all the oil level (hydraulic oil, motor oil, diesel, lubricating oil, air compressor oil).
5. Lubricate the whole machine, especially the propelling beam, the rock drilling part.
6. Replace the oversized rubber guide bushing on the two rotary rods of the propelling beam.
7. Frequently check the water filtering net and remove foreign substances.
8. Discharge the water in the oil tank before starting the jumbo. Replace the hydraulic oil if necessary.
9. In cold weather conditions, it’s necessary to discharge the water pump and the cooling machine to prevent them against frost crack.
10. Fasten loosened parts of electrical wires.
11. Check the voltage and current to see if there is any abnormal condition in each hydraulic pressure indicator.
12. Check the pressure and adjust it if necessary.
B. Regular maintenance of drilling jumbo
1. Check if there is any air and oil leakage.
2. Lubricate the surface of rock drilling machine and energy accumulator.
3. Check the hydraulic oil pipe.
4. Check if there is any water leakage.
5. Fill the gearbox with high temperature grease.
Note:the grease should be Shell EP2 or COP GREASE by Shell or molybdenum disulfide lithium-based grease.
6. Check the testing valve of energy accumulator to see if there is nitrogen gas.
7. Check the head of the rock drilling machine. Fasten the loosened parts as per the required torque.
8. Check the guide bush in the machine head. If the distance between the drill rod and the guide bush is beyond 1mm, replace the guide bush.
9. Maintenance after Running 40 Hours
(1) Fasten all the bolts.
(2) Check the energy accumulator.
(3) Refill the nitrogen gas with 100-bar high-pressure gas and 25-bar low-pressure gas.
10. Maintenance after Running 400 Hours
Overhaul the machine in a clean and dust-free plant. Note: Overhaul can be carried out after running the machine 200 hours if necessary.
C. Maintenance adjustment in particular circumstances
Sometimes we need to adjust the maintenance period and frequency given the different conditions like temperature, humidity, workload, etc. to better protect the machine.
1. A new motor or an overhauled motor that has operated 50 hours
(1) Check if there is any oil leakage.
(2) Check all the bolts of the motor. Use the right torque to check if the bolt is loosened.
(3) Check the tension of the belt.
(4) Replace the diesel oil filter core.
(5) Replace the machine oil filter core.
(6) Replace the machine oil.
2. Maintenance performed as per the running hour of rock drilling machine and the traveling hour of motor
(1) Maintenance after 10 hours’ running
a. Check if the bolts of the propelling beam loose.
b. Check all the oil pipes around the propelling beam to see if there is any leakage and all the bolts are in position.
c. Clean the propelling beam.
d. Check all the oil pipes and bolts of the large arm to avoid leakage or loosening.
e. Check the oil level and pressure of the hydraulic oil tank.
f. Check if the return oil filter core is clogged.
g. Check the respirator.
h. Check if the hydraulic oil pipe is damaged.
i. Check the oil level of the air compressor.
j. Check the water inlet filter core and rinse if necessary.
k. Check the electric cable drum. Spin it at least one time a shift to prevent it from rusting.
(2) Maintenance after 50 hours’ running
a. Grease the oil pipe pulley and propelling pipe pulley.
b. Clean the propelling beam.
c. Fasten the bolts of each connecting plate and propelling beam.
d. Check the tension of the propelling and return rope: 1. eliminate the possibility of the steel wire rope jumping out of the drum. 2. The steel wire rope should not be too tight. 3. The right tension of the drilling jumbo would show a little gap of several centimeters.
e. Check rubber sleeve of the drill rod supporting device. If the wear condition is beyond limit, replace it immediately.
f. Check the abrasion of sliding block of propelling beam and rock drilling machine. The clearance should be around 1-2mm. Adjust the clearance on time if necessary.
g. No grease is allowed on the propelling beam.
h. Lubricate all the parts that need to be greased.
i. Check the grease nipple, and replace the damaged nipple immediately.
j. Fasten all the bolts.
k. Open the hydraulic oil tank and discharge the water inside.
l. Clean the cable drum and fasten its bolts. Check the abrasion.
m. Check the pulley of the propelling beam and the oil pipe. Replace on time if necessary.
n. Check the propelling oil pipe to see if there is any leakage and abrasion.
o. Check the limit switch for abrasion.
p. Check the large arm to see if there is any leakage and abrasion.
q. Replace the respirator if necessary.
r. Check the gearbox oil level of cable drum.
(3) Maintenance after 500 hours’ running
Check the air inlet filter core of the air compressor. Replace it in time, and never used the replaced core anymore.
(4) Maintenance after 1000 hours’ running
a. Replace the return oil filter core of the hydraulic oil.
b. Replace the gearbox oil of the cable drum.
(5) Maintenance after 10 hours’ travelling
a. Check the emergency button.
b. Check the fire extinguisher to see if it’s still at the safe place.
c. Check the oil level of motor.
d. Check the air filter core to see if there is dirt.
e. Check the oil pipe of the cable drum to see if there is any abrasion.
(6) Maintenance after 50 hours’ travelling
a. Check the oil level of the gear box.
b. Check the pressure of the braking system.
c. Lubricate the cable drum.
d. Clean the dirt between battery connections.
(7) Maintenance after 250 hours’ travelling
a. Check the oil level of the main drive and hub. Add oil if necessary.
b. Check the bolt of the transmission shaft.
c. Check the grease.
d. Check the hand brake.
(8) Maintenance after 500 hours’ travelling
a. Check the diesel tank to see if there is any leakage.
b. Check the bolt of motor to see if it is loosened.
c. Replace the oil and filter core of machine.
d. Replace the filter core of the diesel.
e. Check the tension of the belt.
f. Replace the oil and filter core of intermediate gear.
g. Check the foot brake pressure.
h. Check the tension of cable drum chain and change the oil of its gear box.
(9) Maintenance after 1000 hours’ travelling
a. Clean the motor and check the oil pipe connection if necessary.
b. Replace the filter core of the diesel.
c. Check the abrasion of connections of intermediate gear. Replace the connections if necessary.
d. Check the tension of cable drum chain and change the oil of its gear box.
(10) Maintenance after 2000 hours’ travelling
a. Change the oil and filter core of motor, the front and back intermediate gear, gear box, etc.
1. Check if there is any oil leakage.
2. Fasten loosened bolts.
3. Clean the propelling beam.
4. Check all the oil level (hydraulic oil, motor oil, diesel, lubricating oil, air compressor oil).
5. Lubricate the whole machine, especially the propelling beam, the rock drilling part.
6. Replace the oversized rubber guide bushing on the two rotary rods of the propelling beam.
7. Frequently check the water filtering net and remove foreign substances.
8. Discharge the water in the oil tank before starting the jumbo. Replace the hydraulic oil if necessary.
9. In cold weather conditions, it’s necessary to discharge the water pump and the cooling machine to prevent them against frost crack.
10. Fasten loosened parts of electrical wires.
11. Check the voltage and current to see if there is any abnormal condition in each hydraulic pressure indicator.
12. Check the pressure and adjust it if necessary.
B. Regular maintenance of drilling jumbo
1. Check if there is any air and oil leakage.
2. Lubricate the surface of rock drilling machine and energy accumulator.
3. Check the hydraulic oil pipe.
4. Check if there is any water leakage.
5. Fill the gearbox with high temperature grease.
Note:the grease should be Shell EP2 or COP GREASE by Shell or molybdenum disulfide lithium-based grease.
6. Check the testing valve of energy accumulator to see if there is nitrogen gas.
7. Check the head of the rock drilling machine. Fasten the loosened parts as per the required torque.
8. Check the guide bush in the machine head. If the distance between the drill rod and the guide bush is beyond 1mm, replace the guide bush.
9. Maintenance after Running 40 Hours
(1) Fasten all the bolts.
(2) Check the energy accumulator.
(3) Refill the nitrogen gas with 100-bar high-pressure gas and 25-bar low-pressure gas.
10. Maintenance after Running 400 Hours
Overhaul the machine in a clean and dust-free plant. Note: Overhaul can be carried out after running the machine 200 hours if necessary.
C. Maintenance adjustment in particular circumstances
Sometimes we need to adjust the maintenance period and frequency given the different conditions like temperature, humidity, workload, etc. to better protect the machine.
1. A new motor or an overhauled motor that has operated 50 hours
(1) Check if there is any oil leakage.
(2) Check all the bolts of the motor. Use the right torque to check if the bolt is loosened.
(3) Check the tension of the belt.
(4) Replace the diesel oil filter core.
(5) Replace the machine oil filter core.
(6) Replace the machine oil.
2. Maintenance performed as per the running hour of rock drilling machine and the traveling hour of motor
(1) Maintenance after 10 hours’ running
a. Check if the bolts of the propelling beam loose.
b. Check all the oil pipes around the propelling beam to see if there is any leakage and all the bolts are in position.
c. Clean the propelling beam.
d. Check all the oil pipes and bolts of the large arm to avoid leakage or loosening.
e. Check the oil level and pressure of the hydraulic oil tank.
f. Check if the return oil filter core is clogged.
g. Check the respirator.
h. Check if the hydraulic oil pipe is damaged.
i. Check the oil level of the air compressor.
j. Check the water inlet filter core and rinse if necessary.
k. Check the electric cable drum. Spin it at least one time a shift to prevent it from rusting.
(2) Maintenance after 50 hours’ running
a. Grease the oil pipe pulley and propelling pipe pulley.
b. Clean the propelling beam.
c. Fasten the bolts of each connecting plate and propelling beam.
d. Check the tension of the propelling and return rope: 1. eliminate the possibility of the steel wire rope jumping out of the drum. 2. The steel wire rope should not be too tight. 3. The right tension of the drilling jumbo would show a little gap of several centimeters.
e. Check rubber sleeve of the drill rod supporting device. If the wear condition is beyond limit, replace it immediately.
f. Check the abrasion of sliding block of propelling beam and rock drilling machine. The clearance should be around 1-2mm. Adjust the clearance on time if necessary.
g. No grease is allowed on the propelling beam.
h. Lubricate all the parts that need to be greased.
i. Check the grease nipple, and replace the damaged nipple immediately.
j. Fasten all the bolts.
k. Open the hydraulic oil tank and discharge the water inside.
l. Clean the cable drum and fasten its bolts. Check the abrasion.
m. Check the pulley of the propelling beam and the oil pipe. Replace on time if necessary.
n. Check the propelling oil pipe to see if there is any leakage and abrasion.
o. Check the limit switch for abrasion.
p. Check the large arm to see if there is any leakage and abrasion.
q. Replace the respirator if necessary.
r. Check the gearbox oil level of cable drum.
(3) Maintenance after 500 hours’ running
Check the air inlet filter core of the air compressor. Replace it in time, and never used the replaced core anymore.
(4) Maintenance after 1000 hours’ running
a. Replace the return oil filter core of the hydraulic oil.
b. Replace the gearbox oil of the cable drum.
(5) Maintenance after 10 hours’ travelling
a. Check the emergency button.
b. Check the fire extinguisher to see if it’s still at the safe place.
c. Check the oil level of motor.
d. Check the air filter core to see if there is dirt.
e. Check the oil pipe of the cable drum to see if there is any abrasion.
(6) Maintenance after 50 hours’ travelling
a. Check the oil level of the gear box.
b. Check the pressure of the braking system.
c. Lubricate the cable drum.
d. Clean the dirt between battery connections.
(7) Maintenance after 250 hours’ travelling
a. Check the oil level of the main drive and hub. Add oil if necessary.
b. Check the bolt of the transmission shaft.
c. Check the grease.
d. Check the hand brake.
(8) Maintenance after 500 hours’ travelling
a. Check the diesel tank to see if there is any leakage.
b. Check the bolt of motor to see if it is loosened.
c. Replace the oil and filter core of machine.
d. Replace the filter core of the diesel.
e. Check the tension of the belt.
f. Replace the oil and filter core of intermediate gear.
g. Check the foot brake pressure.
h. Check the tension of cable drum chain and change the oil of its gear box.
(9) Maintenance after 1000 hours’ travelling
a. Clean the motor and check the oil pipe connection if necessary.
b. Replace the filter core of the diesel.
c. Check the abrasion of connections of intermediate gear. Replace the connections if necessary.
d. Check the tension of cable drum chain and change the oil of its gear box.
(10) Maintenance after 2000 hours’ travelling
a. Change the oil and filter core of motor, the front and back intermediate gear, gear box, etc.
Related Products
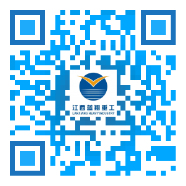