About Us
- Company
- Customers
- Technical Highlights
- Advantages
- Company History
- Environmentally-friendly Facility
- Patents
- Quality Control
- R&D
- Mucking Loader Manual
- Mucking Loader Technical Description
- Mucking Loader Operation Description
- Mucking Loader Maintenance
- Mucking Loader Operation Notes
- Roadheader Manual
- Roadheader Technical Description
- Roadeheader Maintenance
- Roadheader Notes
- Roadheader Operating Method
- Mine Shuttle Car Manual
- Mine Shuttle Car Maintenance
- Mine Shuttle Car Operation
- Mine Shuttle Car Technical Description
- Mine Shuttle Car Notes
- Trolley Locomotive Maintenance
- Maintenance Manual of Drilling Jumbo
- Contact Us
Mucking Loader Maintenance
1. The mucking loader should be always kept complete and clean. Pay special attention to the tunnel to prevent water leak in by covering it with a rubber plate or canvas.
2. Bolts and nuts should be frequently checked and fastened. The missing pin of the chain should be added immediately.
3. Frequently check each hydraulic component and the joints of pipes. Check if the high pressure hose is damaged, and immediately replace it if it’s seriously damaged.
4. Frequently check the oil height and temperature. Refill the oil if the oil level is lower than the indicator. Turn off the machine for a moment if the oil temperature is over 80℃.
5. Regularly check the working pressure of the hydraulic system (one time per month) to avoid any abnormal circumstance.
6. Change the hydraulic oil after running the loader 120 hours, 300 hours and 500 hours. Each time when changing the hydraulic oil, replace the return oil filter core and clean the oil tank and air filter core. From the third time on, the hydraulic oil should be replaced after running the mucking loader 500 hours. Note: clean the oil absorb filter core every month.
7. Add grease to each grease cup every week. Lubricate the connecting pin and shaft every day.
8. Frequently check the crawler belt after running the mucking loader six months. If the abrasion is beyond 5mm, replace it immediately.
9. Regularly check the connecting bolt of track shoe and hydraulic motor. If the bolt is loosened or missed, fasten it or add new bolt immediately.
10. Hard objects like rocks that stuck in the crawler belt chain should be cleaned immediately.
11. If the transporting trough sags more than 150mm, change the chain immediately.
12. Clean the mucking machine each time after loading. It’s better to grease the scraper chain with used oil (the replaced hydraulic oil is ok). This can greatly extend the service life of the chain.
13. Worn-out bucket teeth could be replaced by knocking the elastic pin out.
14. If the position where the bucket teeth is mounted on wear out, welding a new one with 506 or 507 welding rod. Before welding, using gas cutting method to cut the abraded one and then polishing the original welding joint. Direct current is preferred.
15. Replace the abraded drive sprocket as per the following steps: (1) Take apart the chain by knocking out the elastic pin before removing the abraded drive sprocket. (2) Use oxy-acetylene flame to remove the original welding line. (3) Take down the abraded drive sprocket. (4) Mount the drive sprocket on. (5) To fasten the new sprocket, knock in a plastic pin and make its open facing the axis line. (6) Weld this open area using 506 or 507 welding rod. (7) Install the chain.
16. Regularly check the earthing device and explosion-proof equipment. Keep explosion-proof surface with oil to avoid rust.
17. Portable methane alarm apparatus should be equipped in underground coal mines.
18. Check the following lubricating points and fill lubricating oil in as per requirements (please look into following table).
2. Bolts and nuts should be frequently checked and fastened. The missing pin of the chain should be added immediately.
3. Frequently check each hydraulic component and the joints of pipes. Check if the high pressure hose is damaged, and immediately replace it if it’s seriously damaged.
4. Frequently check the oil height and temperature. Refill the oil if the oil level is lower than the indicator. Turn off the machine for a moment if the oil temperature is over 80℃.
5. Regularly check the working pressure of the hydraulic system (one time per month) to avoid any abnormal circumstance.
6. Change the hydraulic oil after running the loader 120 hours, 300 hours and 500 hours. Each time when changing the hydraulic oil, replace the return oil filter core and clean the oil tank and air filter core. From the third time on, the hydraulic oil should be replaced after running the mucking loader 500 hours. Note: clean the oil absorb filter core every month.
7. Add grease to each grease cup every week. Lubricate the connecting pin and shaft every day.
8. Frequently check the crawler belt after running the mucking loader six months. If the abrasion is beyond 5mm, replace it immediately.
9. Regularly check the connecting bolt of track shoe and hydraulic motor. If the bolt is loosened or missed, fasten it or add new bolt immediately.
10. Hard objects like rocks that stuck in the crawler belt chain should be cleaned immediately.
11. If the transporting trough sags more than 150mm, change the chain immediately.
12. Clean the mucking machine each time after loading. It’s better to grease the scraper chain with used oil (the replaced hydraulic oil is ok). This can greatly extend the service life of the chain.
13. Worn-out bucket teeth could be replaced by knocking the elastic pin out.
14. If the position where the bucket teeth is mounted on wear out, welding a new one with 506 or 507 welding rod. Before welding, using gas cutting method to cut the abraded one and then polishing the original welding joint. Direct current is preferred.
15. Replace the abraded drive sprocket as per the following steps: (1) Take apart the chain by knocking out the elastic pin before removing the abraded drive sprocket. (2) Use oxy-acetylene flame to remove the original welding line. (3) Take down the abraded drive sprocket. (4) Mount the drive sprocket on. (5) To fasten the new sprocket, knock in a plastic pin and make its open facing the axis line. (6) Weld this open area using 506 or 507 welding rod. (7) Install the chain.
16. Regularly check the earthing device and explosion-proof equipment. Keep explosion-proof surface with oil to avoid rust.
17. Portable methane alarm apparatus should be equipped in underground coal mines.
18. Check the following lubricating points and fill lubricating oil in as per requirements (please look into following table).
No. | Lubricating Oil | Position | Qty | Maintenance Period |
1 | Grease | Main drive gear bearing of transport trough | 2 | 32 hours |
2 | Grease | Support bearing of drive sprocket | 2 | 8 hours |
3 | Grease | Bearing of small arm’s revolving axle | 2 | 8 hours |
4 | Grease | Supporting axle of bucket | 2 | 8 hours |
5 | Grease | End of large arm support bearing | 2 | 8 hours |
6 | Grease | End of clevis pin | 22 | 16 hours |
Related Products
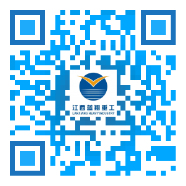